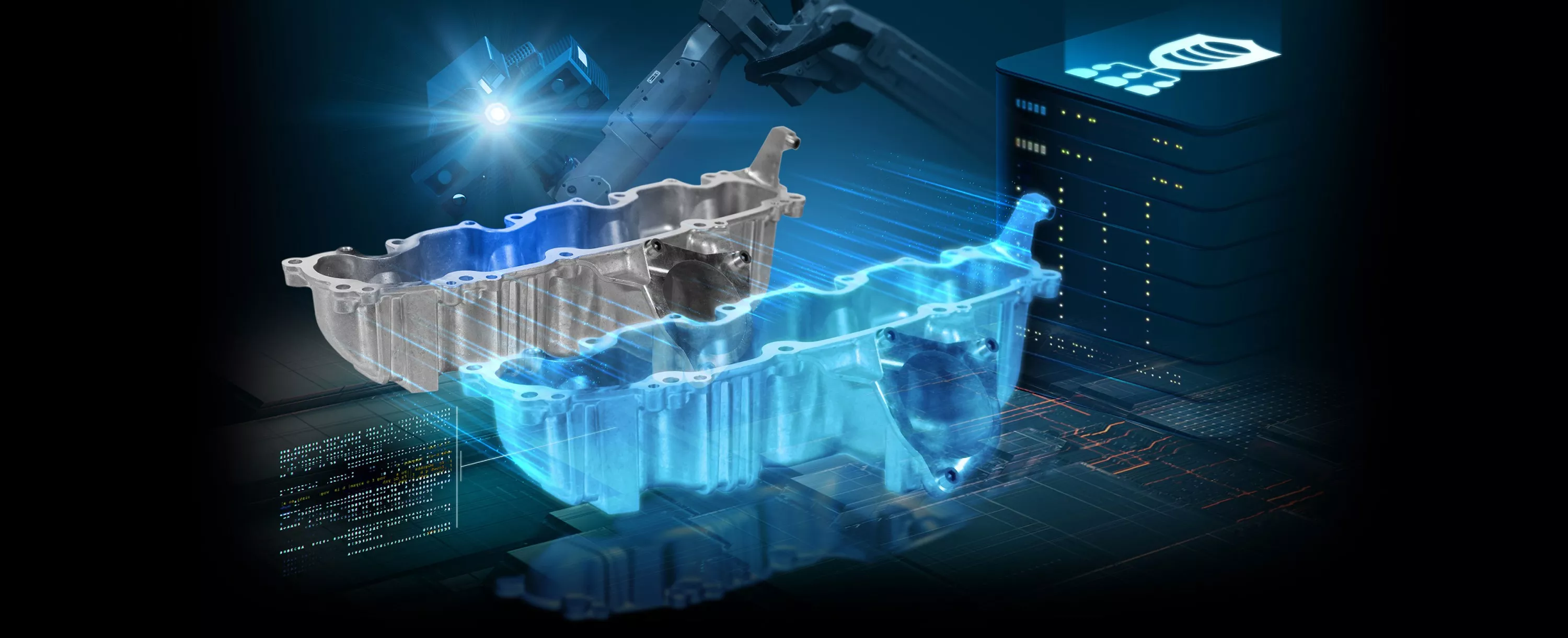
การจัดการข้อมูลและการเชื่อมต่อดิจิทัล
ตรวจสอบและปรับปรุงคุณภาพการผลิตด้วยเทคโนโลยี Digital Twin และการจัดการข้อมูลบนพอยต์คลาวด์
การจัดการข้อมูลและการเชื่อมต่อดิจิทัล
ตรวจสอบและปรับปรุงคุณภาพการผลิตด้วยเทคโนโลยี Digital Twin และการจัดการข้อมูลบนพอยต์คลาวด์
การแสดงวัตถุหรือกระบวนการทางกายภาพแบบเสมือนและการจำลองความเป็นจริงภายในสภาพแวดล้อมเสมือนจริง นำเทคโนโลยี digital twin ไปสู่ความก้าวหน้าในหลายสาขาที่มีความสำคัญ ทั้งการผลิต การก่อสร้าง และการดูแลสุขภาพ Digital twin อิงตามข้อมูลการสแกน 3 มิติ ที่มีความแม่นยำ ทั้งข้อมูลที่ช่วยในการตรวจสอบและปรับปรุงการผลิต ทำให้สามารถใช้งานกระบวนการประกอบและการตรวจสอบคุณภาพแบบดิจิทัลซึ่งช่วยลดต้นทุน เร่งเวลาเปิดตัวสินค้า รวมถึงปรับปรุงรูปแบบ ความพอดี และฟังก์ชันการทำงาน
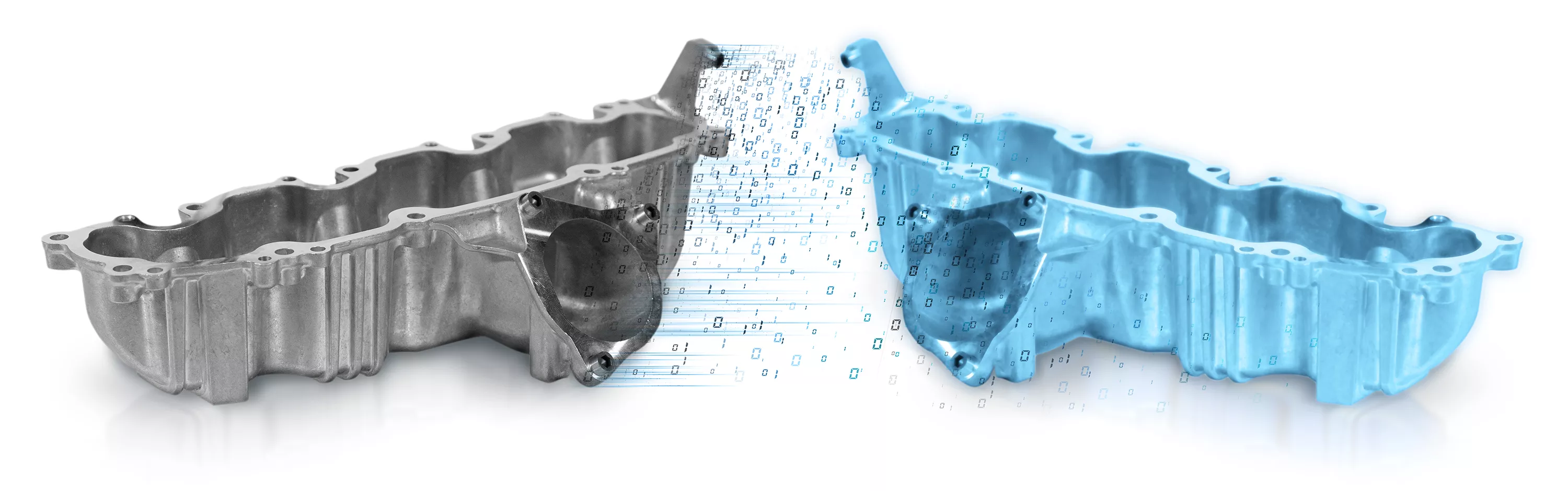
ในโลกของการผลิต Digital Twin Instance (DTI) คือ digital twin ของแต่ละชิ้นส่วนหรือผลิตภัณฑ์ที่ได้จากการผลิต เทคโนโลยีการสแกน
พอยต์คลาวด์สามารถวัดพื้นผิวของชิ้นงานที่ผลิตและผลิตภัณฑ์ที่ประกอบได้อย่างรวดเร็วและถูกต้อง ทำให้เทคโนโลยีนี้เป็นเครื่องมือในอุดมคติสำหรับ
การสร้าง DTI อีกอย่างหนึ่งที่จำเป็นไม่แพ้กันก็คือโซลูชันการจัดการข้อมูลดิจิทัลที่มีประสิทธิภาพในการจัดการโปรเจ็กต์การวัด 3 มิติขนาดใหญ่ต่างๆ ได้อย่างเหมาะสม รวมทั้งสรุปข้อมูลเมตาที่เชื่อมโยงชิ้นงานที่วัดเข้ากับกระบวนการผลิต และแชร์ DTI แบบดิจิทัลไปทั่วทั้งองค์กร
มีใครบ้างที่ต้องการชิ้นงานตัวจริงคืนหลังจากได้สแกนพื้นผิวทั่วทั้งชิ้นแล้ว?
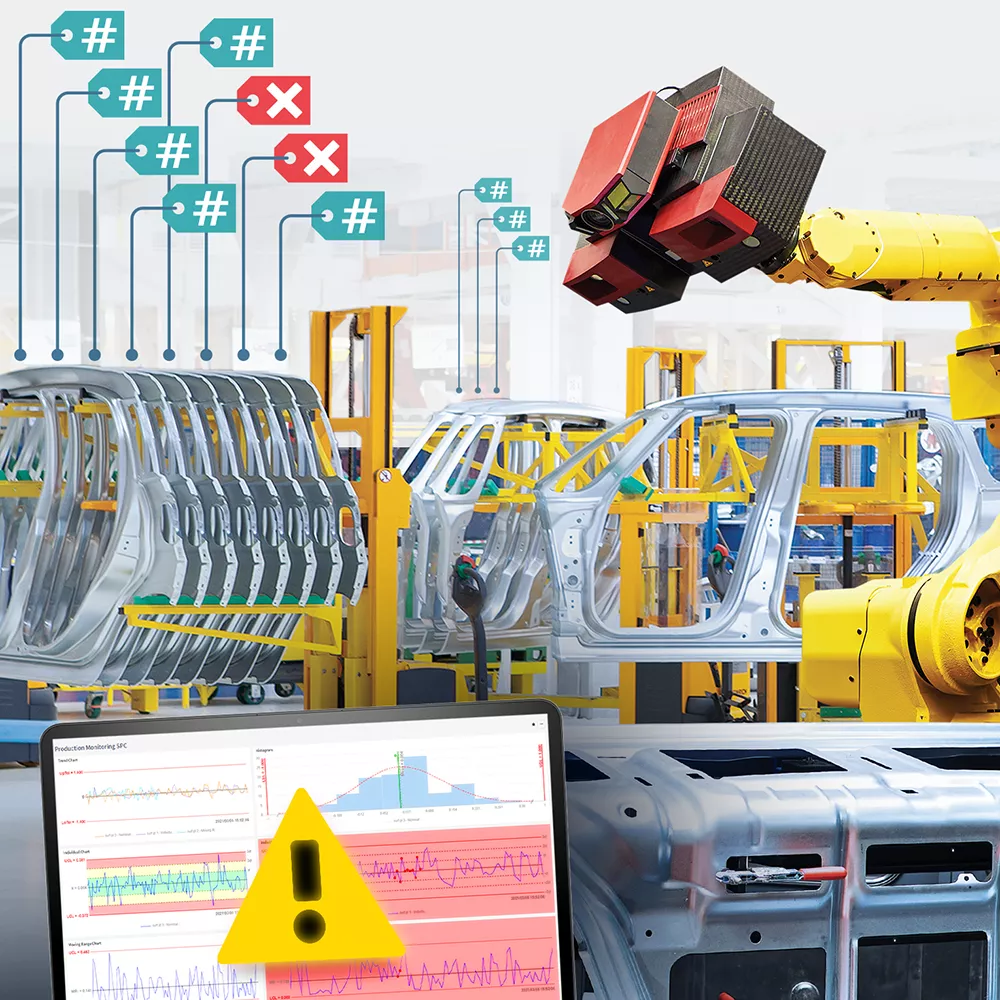
คำตอบคือแทบจะไม่มี หลังจากใช้เครื่องสแกนพอยต์คลาวด์สแกนพื้นผิวของชิ้นงานจริงทั่วทั้งชิ้นแล้ว เราจะสามารถตรวจสอบความถูกต้อง สืบหาสาเหตุของปัญหา และจำลองผลลัพธ์ DTI ที่ได้โดยไม่ต้องกลับมาดูชิ้นงานตัวจริง
ลองนึกถึงกรณีที่เกิดความล้มเหลวในการผลิต การสแกนชิ้นส่วนที่ผลิตทั้งหมดช่วยให้ทีมควบคุมคุณภาพสามารถติดตามย้อนกลับไปยังชิ้นส่วนที่ถูกผลิตในช่วง 24 ชั่วโมงที่ผ่านมา และวิเคราะห์ชิ้นส่วนเหล่านั้นในระบบเสมือน เพื่อที่จะระบุได้อย่างแม่นยำว่าชิ้นงานใดไม่ถูกต้อง และนำออกจากคลังสินค้าก่อนจัดส่ง ซึ่งจะช่วยให้หลีกเลี่ยงการเรียกคืนสินค้าที่มีค่าใช้จ่ายสูงได้
ลองนึกถึง OEM ที่รับข้อมูลสแกนของชิ้นงานต้นแบบจากซัพพลายเออร์หลายราย การประกอบแบบเสมือนช่วยให้ค้นพบว่าซัพพลายเออร์ผู้ผลิตรายหนึ่งได้ใช้โมเดล CAD ฉบับแก้ไขที่ไม่ถูกต้อง จึงมีการติดต่อซัพพลายเออร์รายดังกล่าวทันที และแนะนำให้ใช้การทำซ้ำอย่างถูกวิธีอีกครั้งก่อนการผลิตและการจัดส่ง
หรือลองนึกภาพว่าคุณเป็นซัพพลายเออร์ชิ้นส่วนเครื่องบิน ลูกค้ารายหนึ่งเกิดความไม่พอใจและติดต่อเข้ามาโดยอ้างว่าชิ้นงานที่ซื้อไปมีความคลาดเคลื่อนเกินกว่าจะรับได้ตั้งแต่ตอนที่จัดส่ง แต่โชคดีที่มีการสแกนข้อมูลไว้ก่อนจัดส่ง คุณจึงพิสูจน์ได้ว่าชิ้นงานมีค่าความคลาดเคลื่อนที่ยอมรับได้ ซึ่งหลีกเลี่ยงการทำให้ลูกค้าไม่พอใจ และโอกาสในการถูกฟ้องร้องก็น้อยลงอย่างมาก
ตัวอย่างสุดท้าย ผู้ผลิตอะไหล่ทดแทนสแกนชิ้นงานประกบของผลิตภัณฑ์ใหม่ จากนั้นแปลงข้อมูลสแกนเหล่านี้เป็น NURBS surface และนำเข้าโมเดลที่ทำวิศวกรรมย้อนกลับเหล่านี้ภายในซอฟต์แวร์การจำลอง เพื่อที่จะวิเคราะห์ลักษณะการออกแบบผลิตภัณฑ์ใหม่เมื่อประกอบเข้าด้วยกัน การจำลองดังกล่าวช่วยให้ผู้ผลิตค้นพบและแก้ไขปัญหาเกี่ยวกับขนาดที่อาจทำให้ผลิตภัณฑ์มีความทนทานน้อยลง
ตัวอย่างเหล่านี้ทำให้เห็นภาพว่าการใช้ digital twin มีศักยภาพมากมายในการปรับปรุงกระบวนการและลดค่าใช้จ่าย ทั้งในกระบวนการออกแบบ วิศวกรรม การผลิต และการบำรุงรักษา
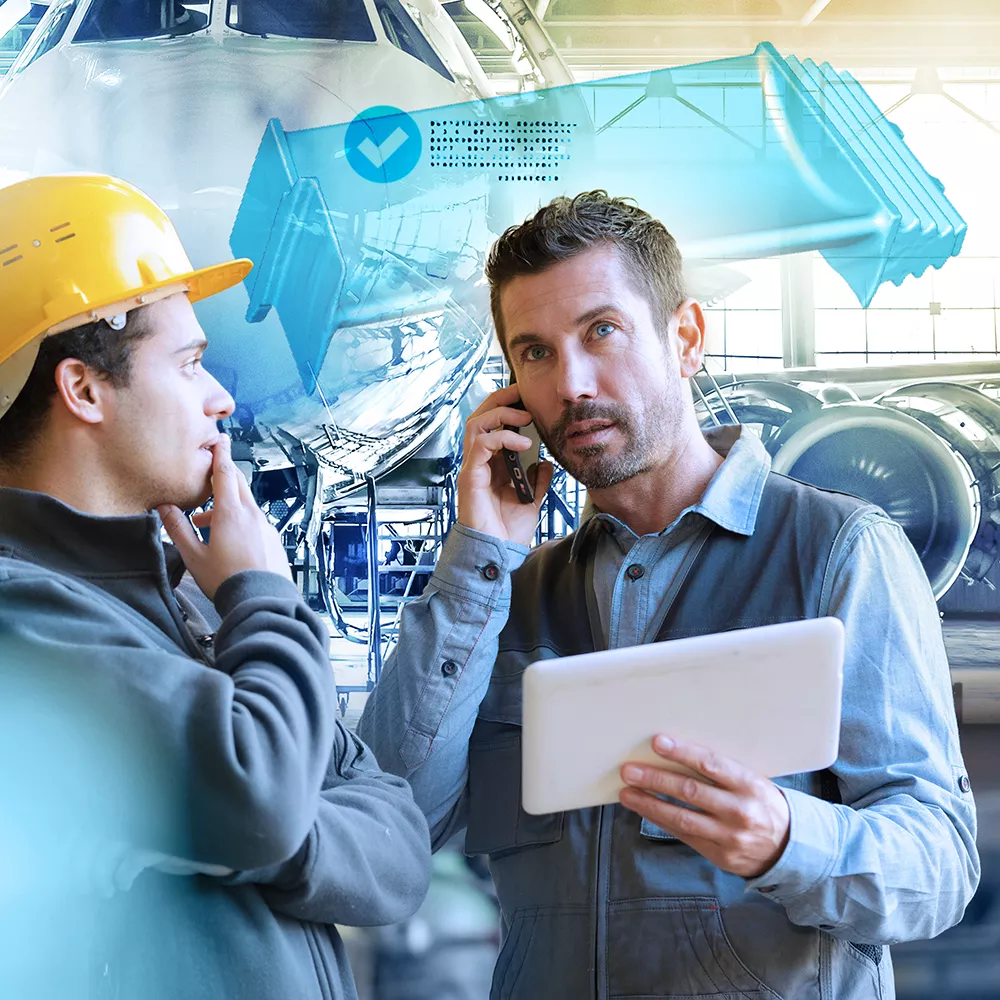
ความท้าทายในการนำกระบวนการ Twin digital
ที่อยู่บนพอยต์คลาวด์ไปใช้ในการผลิต
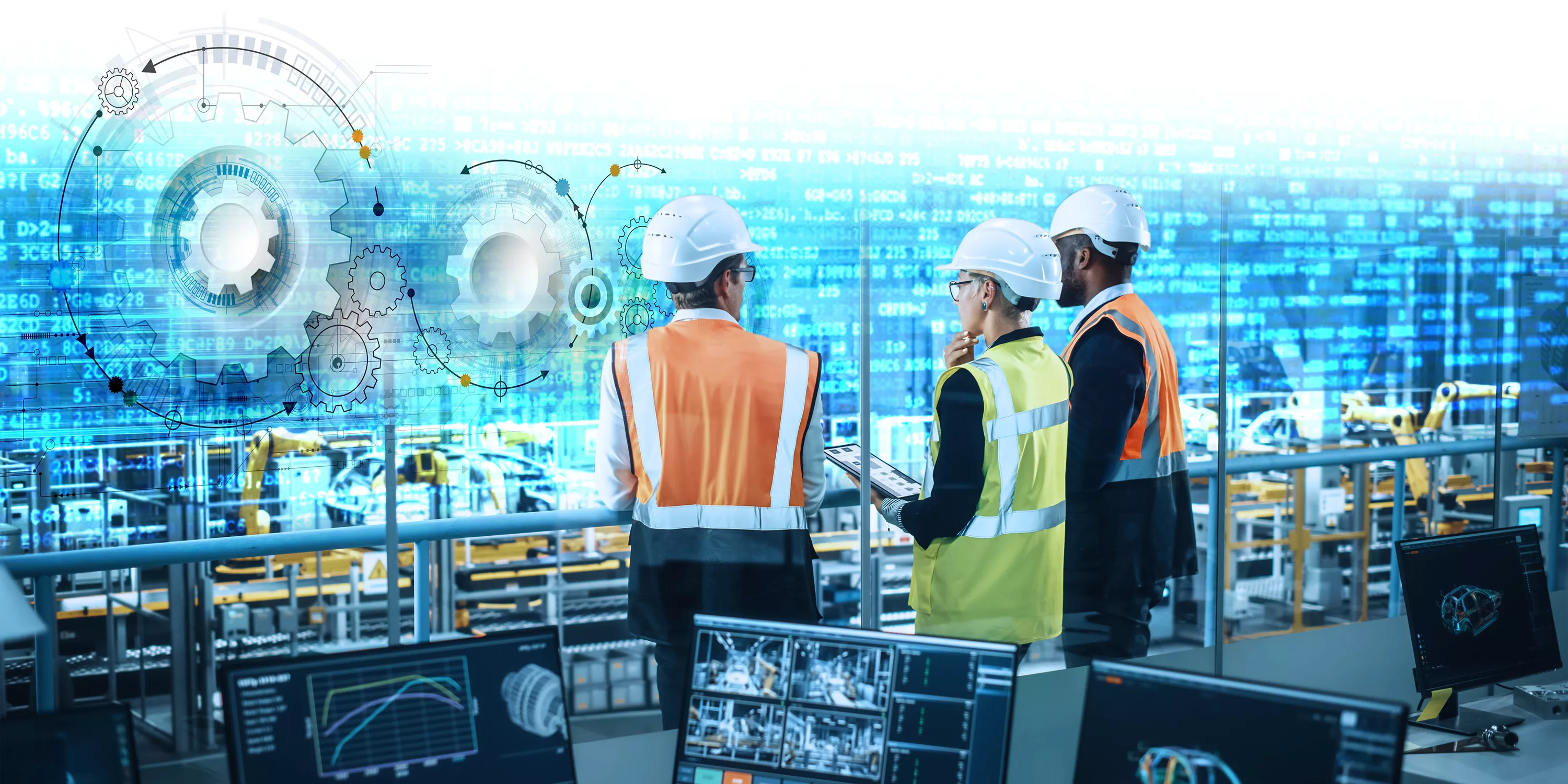
แม้ว่า DTI จะมอบศักยภาพที่ยิ่งใหญ่ให้กับองค์กรการผลิต แต่ก็ยังมีความท้าทายในการนำกระบวนการ digital twin ไปใช้กับโมเดลที่สร้างจากข้อมูลพอยต์คลาวด์
ช่วยในการจัดการไฟล์ เครื่องสแกนพอยต์คลาวด์ผลิตข้อมูลได้หลายเมกะไบต์ต่อหนึ่งวินาที หลังจากแปลงข้อมูลดิบพอยต์คลาวด์เป็นข้อมูลโพลิกอน
ที่ถูกต้องซึ่งแสดงพื้นผิวที่วัดมาได้ ไฟล์ชิ้นงานที่วัดแค่ไฟล์เดียวอาจมีข้อมูลหลายร้อยเมกะไบต์ ลูกค้าที่วางแผนจะสแกนผลลัพธ์ของสายการผลิตอาจต้องจัดการกับไฟล์หลายหมื่นไฟล์และข้อมูลใหม่หลายเทระไบต์ในแต่ละปี การจัดการกับข้อมูลปริมาณมากดังกล่าวด้วยตนเองอาจเป็นเรื่องยากเกินกว่าจะนึกออก
นอกจากนี้ยังมีการตรวจสอบย้อนกลับ ซึ่งต้องเชื่อมโยงโมเดลที่สแกนกับข้อมูลสำคัญๆ ที่เกี่ยวข้องกับชิ้นงานที่วัด รวมไปถึงกระบวนการผลิตและ
การวัดต่างๆ อย่างเช่น serial number, หมายเลขชิ้นส่วน, ID อุปกรณ์การวัด, สายการผลิต, ชื่อผู้ปฏิบัติงาน ฯลฯ สำหรับการปฏิบัติงานด้านการผลิตและการบำรุงรักษาแล้ว ข้อมูลเมตานี้มีความสำคัญมากต่อความสามารถในการตรวจสอบย้อนกลับ เพราะช่วยให้จับคู่ DTI กับชิ้นส่วนจริงที่เป็นคู่กันได้อย่างชัดเจน
การแชร์และการทำงานร่วมกันก็อาจเป็นความท้าทายได้เช่นกัน เทคโนโลยีการสแกนมีประสิทธิภาพสูง แต่ถ้าพนักงานที่น่าจะได้รับประโยชน์สูงสุดจากข้อได้เปรียบของกระบวนการนี้ไม่สามารถเข้าถึง DTI ที่ต้องการได้อย่างง่ายดาย ก็มีความเป็นไปได้ว่าพวกเขาจะไม่นำมันมาใช้เลย นำข้อบกพร่องออกเพื่อใช้ประโยชน์ได้อย่างเต็มที่
ระบบจัดการข้อมูลดิจิทัลเพื่อการใช้ digital twin
อย่าง
ประสบความสำเร็จ
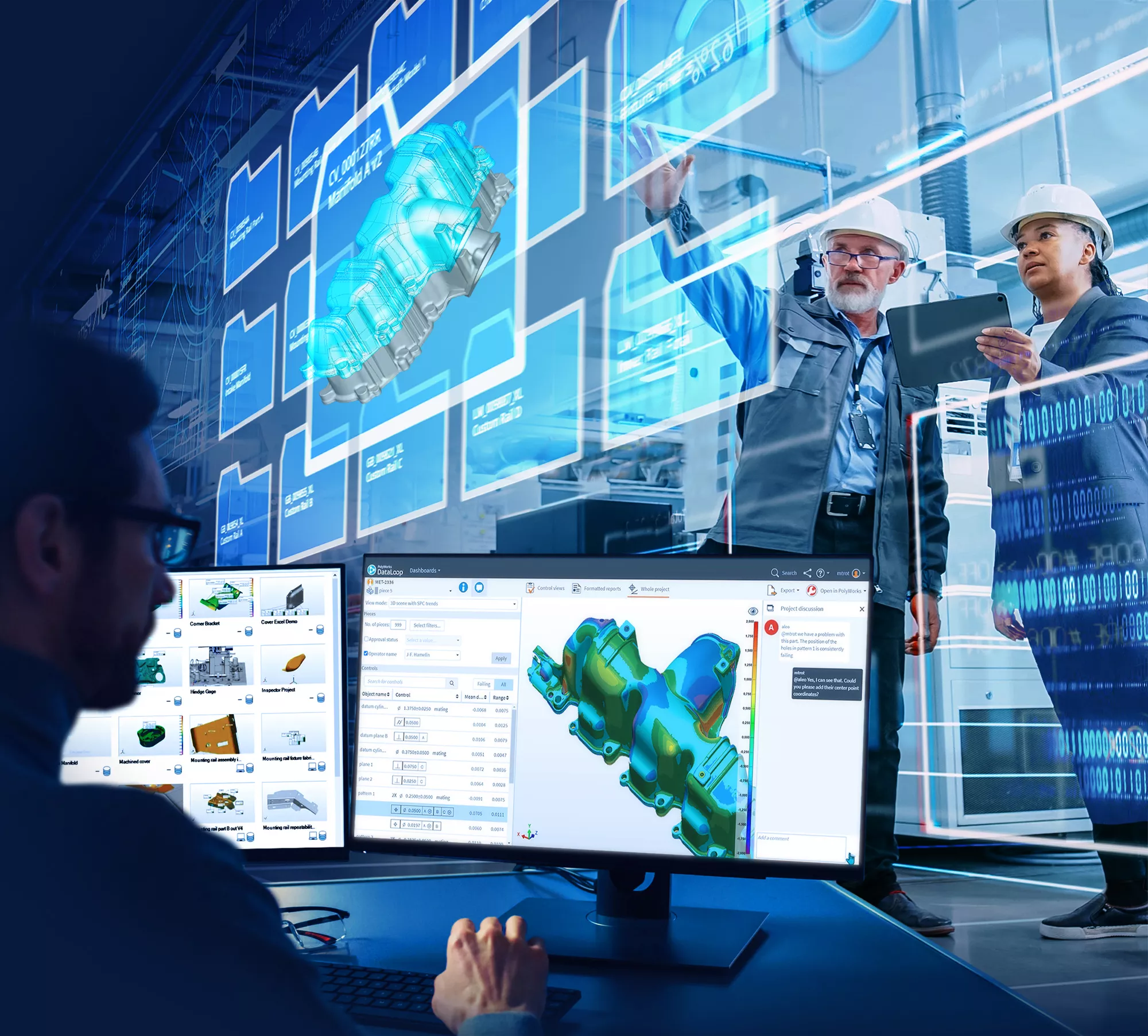
เราจะขจัดปัญหาได้อย่างไร คำตอบคือ โดยการปรับใช้ระบบจัดการข้อมูลดิจิทัลที่พัฒนาขึ้นเพื่อจัดการโปรเจ็กต์และ DTI ขนาดใหญ่ เพราะนอกจากจะไม่ต้องใช้ฮาร์ดไดรฟ์ภายในเครื่อง แต่จัดเก็บข้อมูลการวัด 3 มิติไว้ในเซิร์ฟเวอร์กลาง ระบบการจัดการข้อมูลดิจิทัลนี้ยังทำสิ่งต่อไปนี้ได้ด้วย:
-
ทำให้การจัดการไฟล์และโฟลเดอร์เป็นแบบอัตโนมัติ จึงไม่ต้องใช้โปรแกรมจัดการไฟล์
-
รับรองความปลอดภัยและความสมบูรณ์ของข้อมูลไปพร้อมๆ กับอำนวยความสะดวกในการสำรองข้อมูล
-
เชื่อมโยงแต่ละ DTI กับข้อมูลเมตาสำคัญที่อธิบายถึงชิ้นงานจริงที่เกี่ยวข้องกับกระบวนการผลิตที่ใช้ในการผลิตชิ้นงานและกระบวนการวัดที่ใช้ในการผลิต ทำให้เกิดการสร้างและการรับรองความสามารถในการตรวจสอบย้อนกลับของฝาแฝดดิจิทัลแบบครบวงจร
-
ช่วยให้ทั้งองค์กรสามารถเข้าถึง DTI ผ่านทางเครื่องมือค้นหาที่
ค้นพบ DTI ได้อย่างรวดเร็วโดยใช้คีย์เวิร์ดข้อมูลเมตา -
จัดการสิทธิ์การอนุญาตให้ควบคุมผู้ที่มีสิทธิ์เข้าถึงและสิ่งที่สามารถทำได้กับข้อมูล
หากต้องการเพิ่มประสิทธิภาพของระบบจัดการข้อมูลดิจิทัล องค์กรควรพิจารณาสร้างกลยุทธ์ข้อมูลเมตาที่มีการระบุข้อมูลสำคัญเกี่ยวกับชิ้นงานที่วัดและกระบวนการที่ควรจัดเก็บไว้ในโปรเจ็กต์การวัด
การสแกนพอยต์คลาวด์ + ระบบจัดการข้อมูล = กระบวนการ digital twin ที่ปรับขนาดได้
องค์กรที่ต้องการใช้กระบวนการ digital twin แบบพอยต์คลาวด์อย่างกว้างขวางในอนาคต ควรใช้ระบบจัดการข้อมูลดิจิทัลอย่าง PolyWorks|DataLoop™ จาก InnovMetric มาปรับใช้เพื่อให้แน่ใจว่ากระบวนการของตนมีความสามารถในการปรับขนาดได้ มีเพียงระบบจัดการข้อมูลเท่านั้นที่สามารถจัดการไฟล์หลายหมื่นไฟล์ และเก็บรักษาข้อมูลเมตาอันล้ำค่าที่จะบอกว่าข้อมูลนี้มาจากไหนและถูกสร้างขึ้นมาได้อย่างไร ระบบในลักษณะนี้จะช่วยปรับปรุงประสิทธิภาพของทีมโดยช่วยให้ผู้ใช้งาน digital twin สามารถดึงข้อมูลจากระบบได้ด้วยตนเอง โดยไม่ต้องมีคำแนะนำจากผู้ผลิตข้อมูล
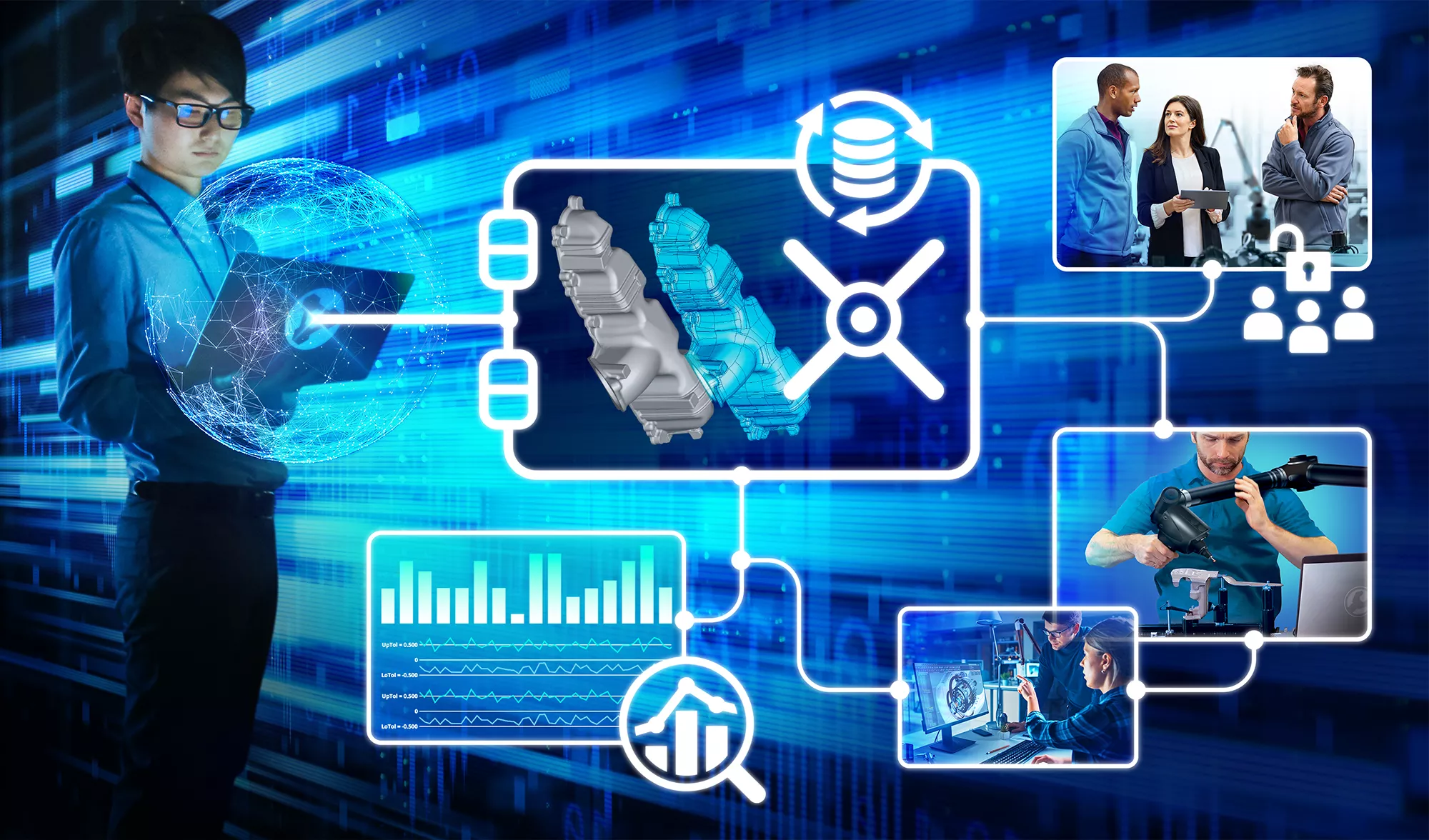
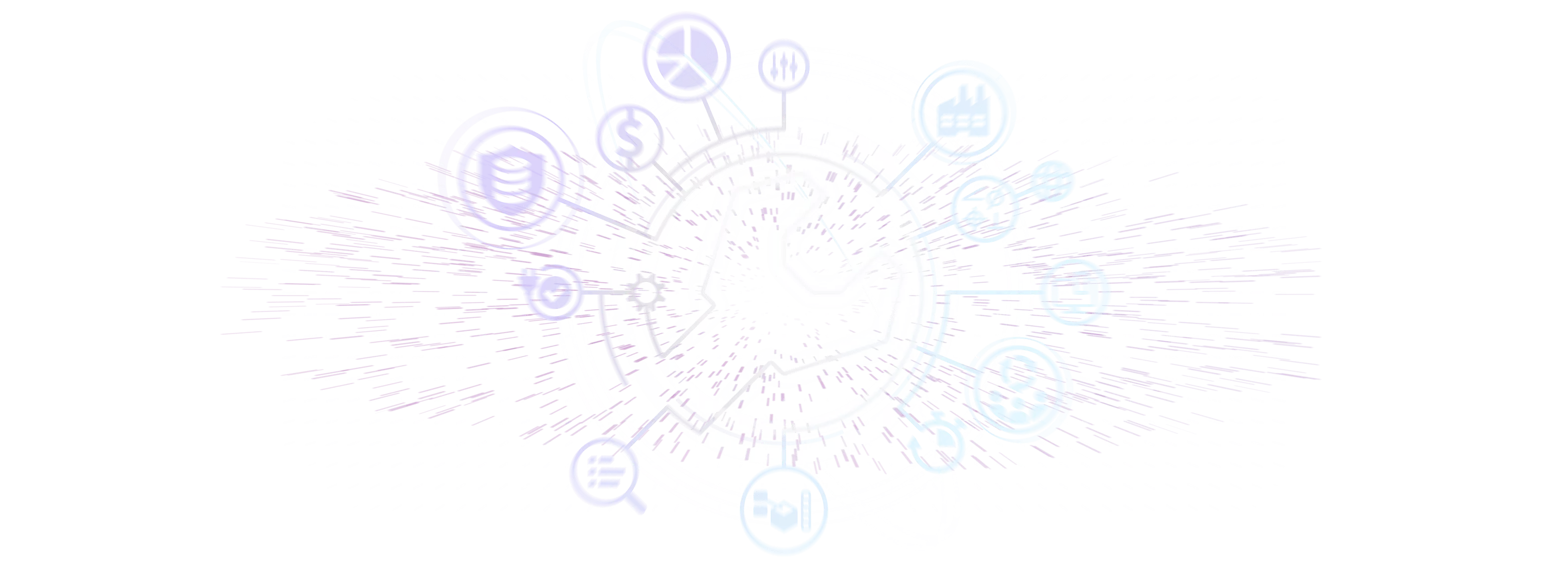
พบกับพลังแห่งการเปลี่ยนแปลงของเทคโนโลยี digital twin และการจัดการข้อมูลแบบครบวงจรสำหรับองค์กรของคุณ
PolyWorks|DataLoop คือโซลูชันการจัดการข้อมูลแบบปรับขนาดได้ ซึ่งจะช่วยอำนวยความสะดวกให้กับการเข้าถึงข้อมูลการวัดที่ได้จาก
แหล่งข้อมูลการวัดหลายแหล่ง (CNC CMM เครื่องสแกนด้วยเลเซอร์ ฯลฯ) ที่พร้อมให้วิศวกรและผู้มีอำนาจตัดสินใจทั่วทั้งองค์กรของคุณนำไปใช้งาน
ทำให้ตัดสินใจได้ดีขึ้นและรวดเร็วยิ่งขึ้น